Making Battery Cables
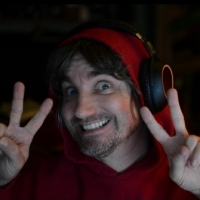
I can't take credit for this method, but it does work well, I'm doing it, so might as well write it up.
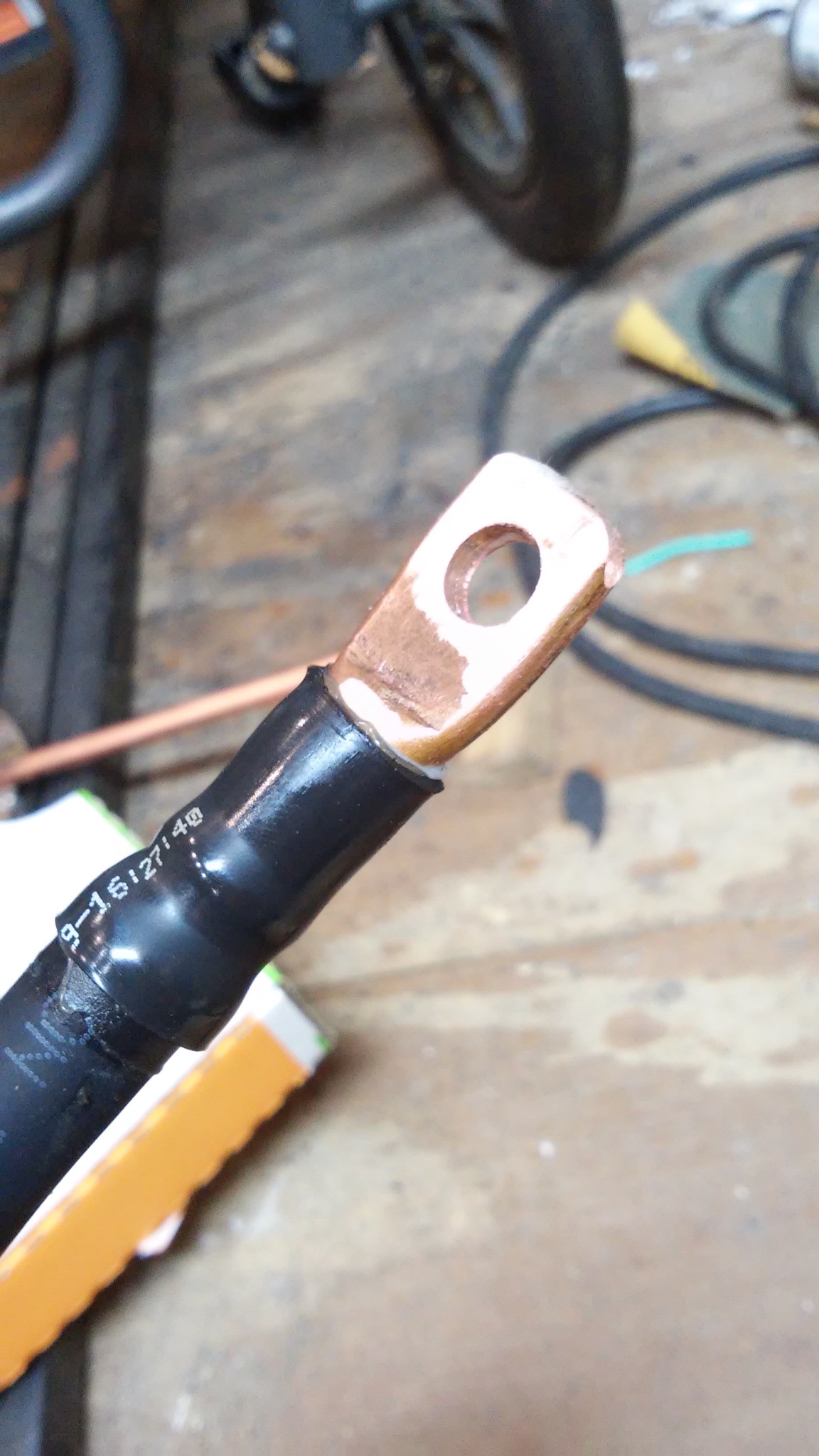
This method is for the battery cables that attach via a bolt or a stud and a nut. The use of copper tubing here is much more effective as the pre made ends cost probably 100x more than what you can make these for.
So the first thing you'll want to do is cut a piece off that is going to make your new end. I am using 3/8 OD copper tube that I picked up from Home Depot. It's meant for refrigerator coolant lines.

The wire I am using is welding cable, I got some in 4 gauge and in 2 gauge. The 4 gauge fits in this perfectly. The 2 gauge I had to flare out a bit, but once flared it's easy to get all of the wires in.

Just tap it lightly onto the swage. Being soft copper it won't take much force. This here was enough to get everything fit.

You can see how the 2 gauge wire will now go in with ease. You might have the one off strand sticking out but it's easy enough to get them back in there if you pay attention.

Then you want to strip the insulation back a bit longer than the new end fitting. This is so the wire can actually stick out the other end. Hit it with a bit of flux.

The flux will help keep the thin wires pasted together when you insert them into the fitting. Like so.

Then comes the hammer. Smash a good bit of the end. You want enough flat that there is ample room for the hole and enough clearance for any washers and bolt heads that will be installed.

Smash.

Now to solder the connection. I like to heat the end and flow the solder in from the other side of the fitting. It will wick it's way through any voids and come out the other end.
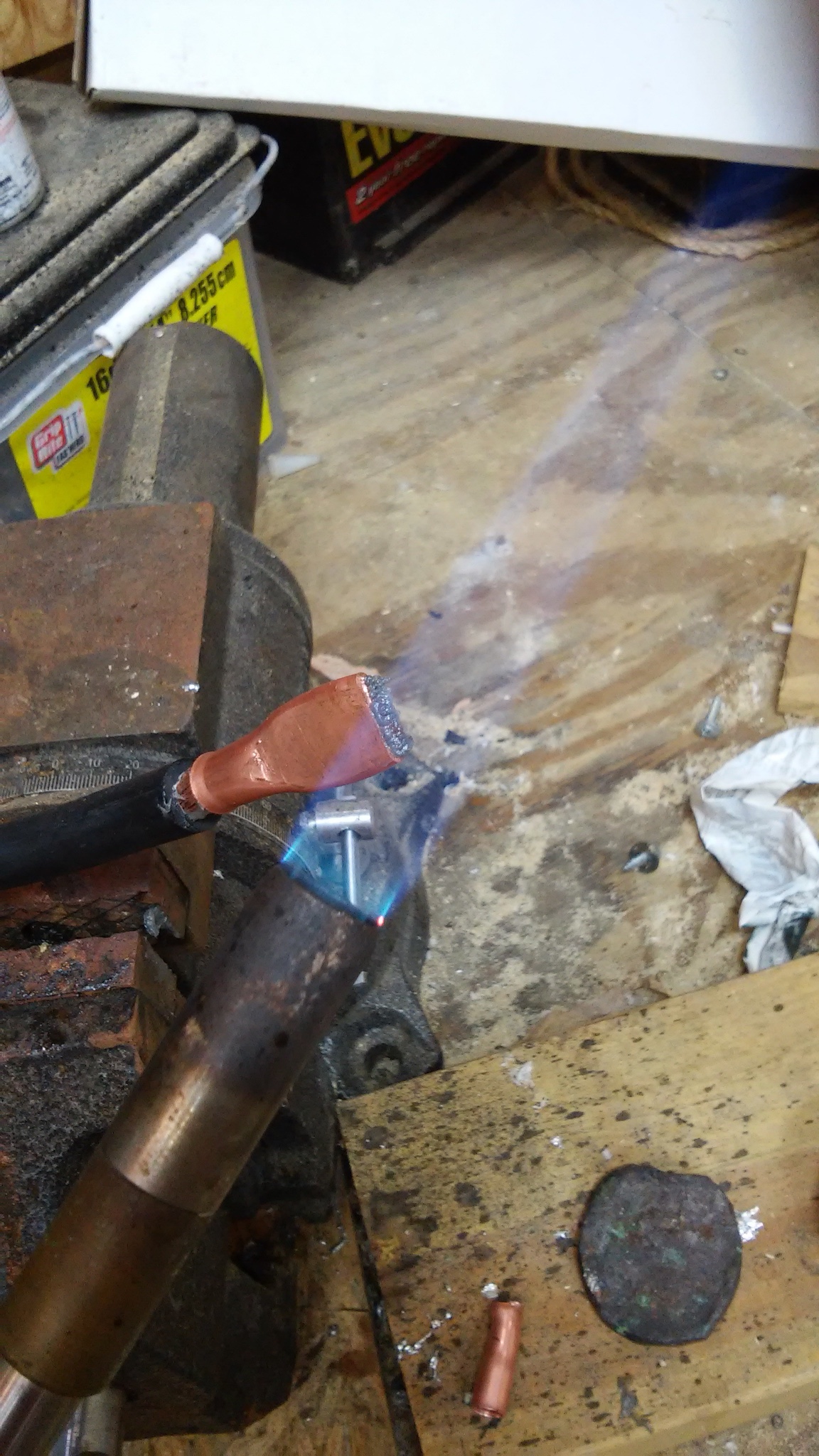
And here it is soldered. It'll get prettier.

Drill the appropriately sized hole through. I recommend center punching the terminal end so you stay on track with the bit.

Here we are all drilled out.

I then shaped the end a bit on the belt sander, nothing too fancy. If you want to take the time to smooth it all out and polish it shiny, go for it.
Then we are going to take some dielectric grease and cover the exposed wire.

Then apply heat shrink tubing. Some people don't like the heat shrink on their battery leads. I'm not one of those people. Also this helps smush the dielectric grease into any voids in the wire at the connection.

And done. Now it's just a matter of repeating this as needed for however many connections and cables you need.
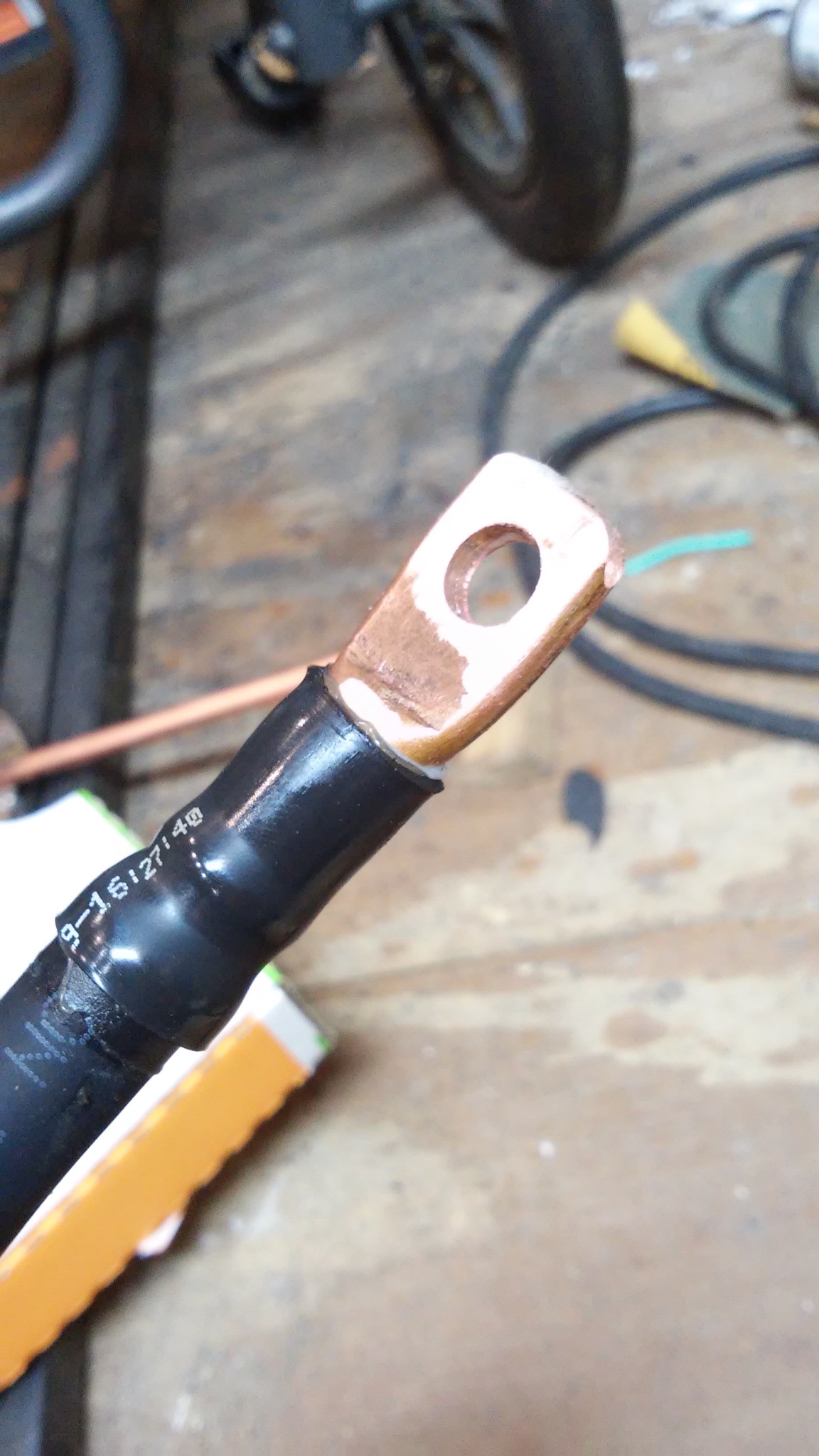
This method is for the battery cables that attach via a bolt or a stud and a nut. The use of copper tubing here is much more effective as the pre made ends cost probably 100x more than what you can make these for.
So the first thing you'll want to do is cut a piece off that is going to make your new end. I am using 3/8 OD copper tube that I picked up from Home Depot. It's meant for refrigerator coolant lines.

The wire I am using is welding cable, I got some in 4 gauge and in 2 gauge. The 4 gauge fits in this perfectly. The 2 gauge I had to flare out a bit, but once flared it's easy to get all of the wires in.

Just tap it lightly onto the swage. Being soft copper it won't take much force. This here was enough to get everything fit.

You can see how the 2 gauge wire will now go in with ease. You might have the one off strand sticking out but it's easy enough to get them back in there if you pay attention.

Then you want to strip the insulation back a bit longer than the new end fitting. This is so the wire can actually stick out the other end. Hit it with a bit of flux.

The flux will help keep the thin wires pasted together when you insert them into the fitting. Like so.

Then comes the hammer. Smash a good bit of the end. You want enough flat that there is ample room for the hole and enough clearance for any washers and bolt heads that will be installed.

Smash.

Now to solder the connection. I like to heat the end and flow the solder in from the other side of the fitting. It will wick it's way through any voids and come out the other end.
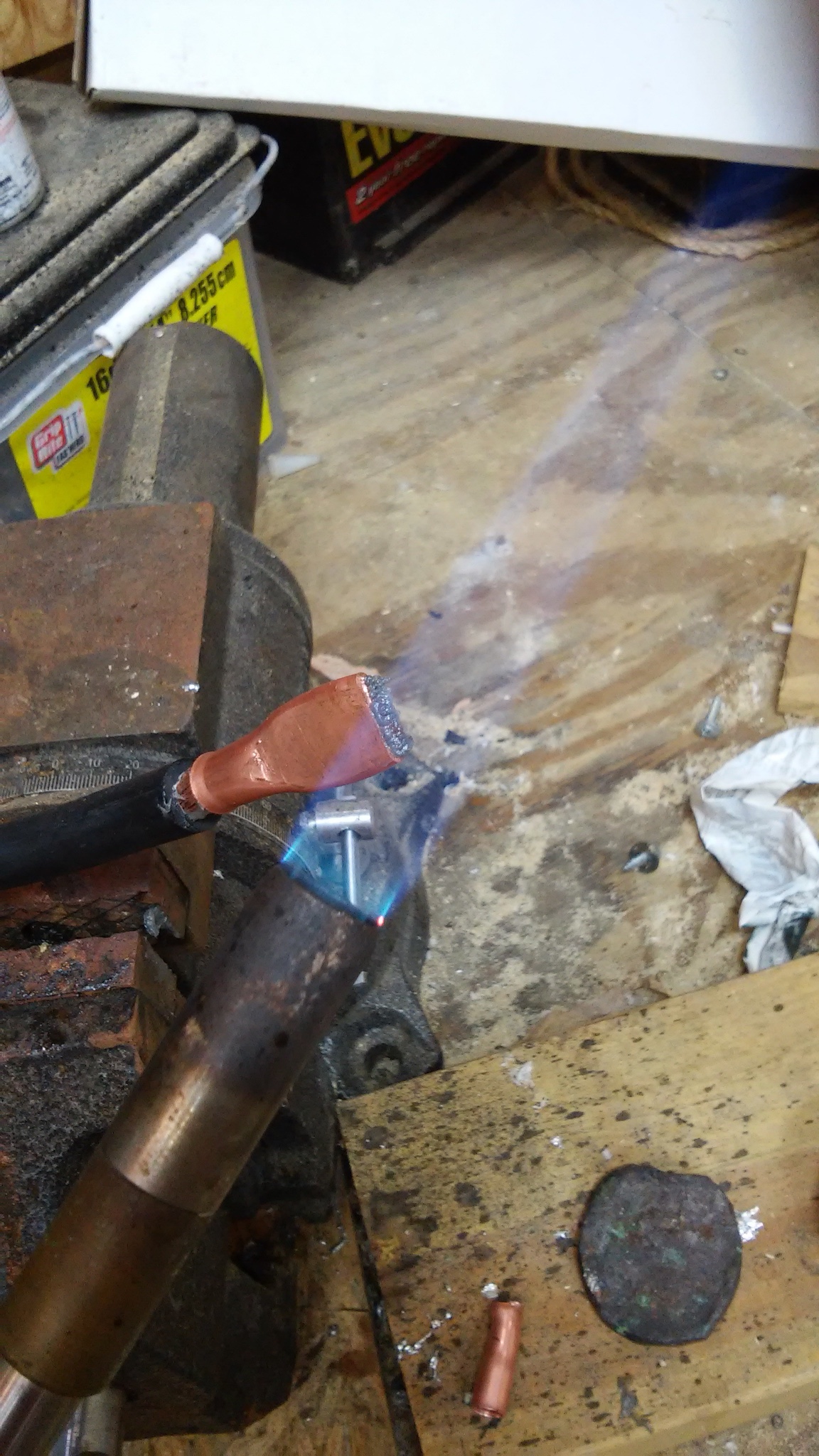
And here it is soldered. It'll get prettier.

Drill the appropriately sized hole through. I recommend center punching the terminal end so you stay on track with the bit.

Here we are all drilled out.

I then shaped the end a bit on the belt sander, nothing too fancy. If you want to take the time to smooth it all out and polish it shiny, go for it.
Then we are going to take some dielectric grease and cover the exposed wire.

Then apply heat shrink tubing. Some people don't like the heat shrink on their battery leads. I'm not one of those people. Also this helps smush the dielectric grease into any voids in the wire at the connection.

And done. Now it's just a matter of repeating this as needed for however many connections and cables you need.

Comments
A perfect crimp will leave the strands looking like a solid block of copper if you were to have a cross section view of it, the method you have given will still leave individual strands with space in between them, it is this space that can have arcing under high load causing the issues.
For the sake of a couple dollars for a real cable lug and taking the cable down to a local electrical supplier which will have a set of real crimpers I cant see why you would bother taking short cuts
It's like the soldering battery cable repair kits. Drop the plug into the terminal, heat it up, dunk the bare wire end in it's done all the time.
Either way, I cut that connection apart and am looking for the individual strands with space between them.
At the fat bit.
And the hammered to hell tab, barely any solder to be found in there. Maybe someone could point out the spaces between the wires for me.
very cool how much did it all cost? or did i miss that part?
are there any benefits from doin this other than saying you did it your self?
"because i do believe in doing things your self if you can because, you'll know its done right. and you will know it wasnt made in china"
and im being totally serious and i just threw the quotes and the pic in because its funny.
If I did that might has swayed my decision to do it this way, but probably not. I like being able to make things myself and pretty much for the reasons that Ron Swanson would agree with.
I like being able to make the cable exactly to fit my needs while being there at the car. I can see exactly what length I need it to be and make sure my terminals are just right. If I had to take it to an electric shop and get it crimped there it might not turn out how I want and I hate when I can place blame on someone other than myself.
So yeah DIY all day.
And also, keep in mind, the flow of power within these types of cables aren't too crazy high, and arcing, while possible, is a tiny concern given that currant likes to travel on the outer most part of any conductive wire, leaving the center closely untouched. So assuming the inner wiring may look ratty, its a lesser concern. If car companies were concerned with arcing because of "high power," they would use waveguides.
For the most part just made it harder to hammer down though and didn't feed as snugly, though perhaps it would reflow nicely when it's heated back up to solder it in the terminal itself. I was pleasantly surprised with the cross section cuts on this especially the smashed down end, it got that stuff together tight, and in the nonflattened part you can make out where the solder filled any voids.
Either way my old battery cable was a screw on replacement that was simply clamped on to the old broken off stock cable. So damn near anything is an improvement over that =D
Also since I'm in to this for maybe $80 all said and done, and just a ground wire set from rywire is $60 I'd say DIY on this is a very good and relatively simple mod.
Another reason for the DIY is I'm going with larger wire, and plan on running a larger ampacity alternator. So this is sort of like the Big 3/4 upgrade.
Then like I said to Klum, I love DIY. If I can do it, I'll do it, and I generally enjoy that type of stuff.
That and something to add a bit more knowledge to the forum here. A big part of the taking pictures anything like that is just to be able to post little write ups here. This might not be one for everyone, if you have concerns like NZ-DB8R has and the cross sections that I took pictures of don't address those concerns, by all means, look for another solution here. Myself I know that I've done this and take pride in that.
Battery to starter 17"
Comparison to original. A little extra length is needed as the heavier gauge wire isn't as flexible.
Also I ran out of heat shrink for one end but I'll sort that tomorrow.
My B if it was mentioned...
I see what NZ-DB8R is talking about, but not too not everyone has a huge crimp set at their disposal and they're not too cheap either.
http://www.amazon.com/gp/product/B005V9V2BG/ref=oh_aui_detailpage_o00_s00?ie=UTF8&psc=1 buncha lugs $15
I put in a high output alt this weekend and needed to make a new hot wire to the battery. Figured i would redo the grounds while i was at it with some 4g. the crimper has a spring that locks the lug in place. you just hold pressure on the wire side and smack it a few times and then rotate so it folds the corners in. Looks just like a machine did it and you're going to cover in heat shrink anyway.
This method looks fine too. though some say solder will get brittle with the vibration and heat cycling.
I did have a break in a wire but it was at a joint that I had made too thin, I figured it was going to go, and it did. So I redid it and left the actual flat part of the terminal thicker.
That particular forney crimper is all right, but like Duke was saying, one that crimps from all sides at once goes for a hell of a lot more and there's a bit of a science to the crimp as well. Crimp too little and you get air pockets, crimp too much and things bulge out and you get less overall capacity. Though we're not running anything mega high amp so I'm sure most of this is all just placebo.
Either way, if the solder joints get brittle and break, I'll be sure to post about it and revisit my strategy on it. I figure since I only have a couple places where any massive vibration occurs those will be the points to look out for, and I have enough wire there that it should help absorb that stress. That break I mentioned was also in part to me having too short of a run of wire there.
Oh, on a quick side note. I got 20 feet of copper tube 3/8" OD at the home depot for $30 and probably paid too much, not sure the length on those terminals you listed, but I think you probably come out ahead on the spool of tube. Also that diameter fits 2# gauge quite snugly, I have to flare out the end a bit more to get all the strands in, and to fit 4# it just needs flared a bit. So it's nice being able to fit that range of wire without having to get a bunch of different terminals.
I agree though, for our cars even the worst of wrong ways would still keep it running another 10 years as long as that valve cover is still grounded (got my second wagon for $500 because that was broken and it "wouldnt start")
Awesome on the score because of bad grounding. I was a victim to that, well an ex girlfriend was. I didn't know much about cars and there was a bad ground that caused the main fuse to pop. Dude looked at things offered a minimal amount of money. She accepted he then secured the ground, replaced the fuse and drove off.